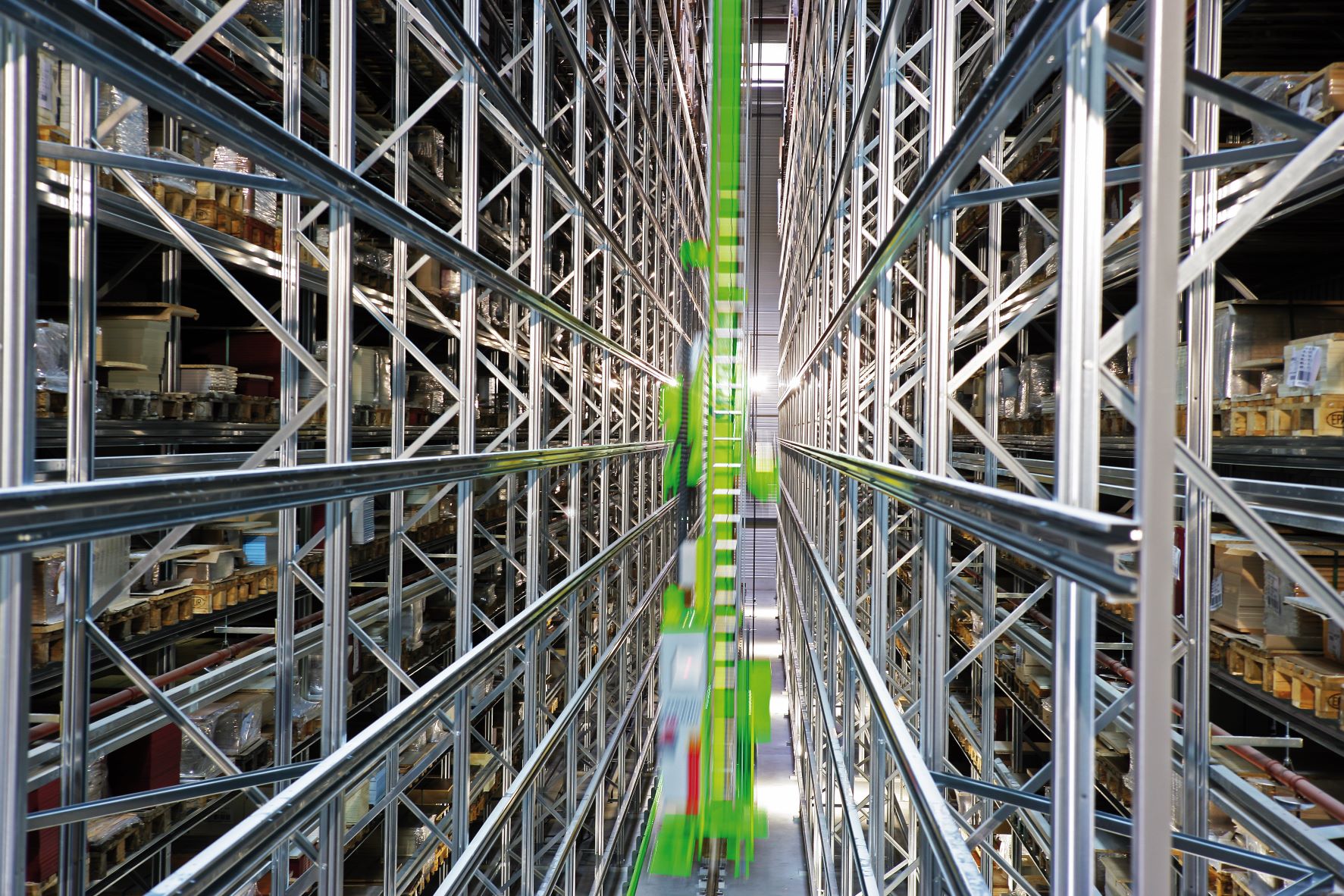
We see it every day at the gas pump and on our utility bills — energy costs are higher now than in recent years. During the last five years alone, energy costs have grown by almost 17%.
Given climate change and political challenges around the world, there is a drive to move away from non-renewable energy sources. However, non-renewable sources still make up more than 80% of all energy used in the US.
So how can your distribution center save energy and money while contributing to a greener future?
Start with the low-hanging fruit. There are many areas of an automated DC where few if any staff are required or only visit on rare occasions. These are known as “lights-out” areas and because the AS/RS doesn’t need light to perform its duties there is no need for illumination. Reducing or eliminating the need for lighting and the associated electricity usage not only lowers costs but can improve climate control efficiency in many cases.
Another low-hanging fruit can be found in the HVAC systems. In ambient warehouses, a fully-automated area means that little or no air-conditioning or heating, which lowers energy requirements and saves money. In cold storage facilities, there are still reduced energy costs because the loss of expensive cooled air is substantially lowered by not having employees going in and out.
Next, stacker cranes and other AS/RS components can regenerate energy to lower the energy use in the DC. With regenerative energy, when a crane begins high and then moves to a lower position, the motor feeds energy back into the system to power the crane down the aisle. Power is also generated from the braking process and that energy is fed back into the lifting motor. Also, the analytics of the system calculates the optimal time when the second drive is activated based on movements and braking point, which delivers the most efficient use of the AS/RS.
A key element to energy efficiency effects is software that has the respective algorithms to control the drives of the AS/RS in the most energy-efficient way. In addition, state-of-the-art software with Warehouse Management and Material Flow Control System can rearrange the inventory inside an AS/RS, for example during low operational activities and/or during night shifts when power is less expensive, and to place certain products in more favorable locations. This has two positive effects. First, due to an optimal location of products being closer to the pick-up and drop-off points for the AS/RS, the warehouse throughput will be increased. And secondly, due to closer locations, the drive paths of the AS/RS are shorter which means less energy is needed.
Automation means a smaller footprint is required for the distribution center and that means land costs are lower. Instead of a multi-million square foot DC, companies can reduce that cost tremendously and can often locate the facility closer to hubs of transportation to minimize extra spending on transportation costs. This also impacts the carbon footprint.
Last but not least is put-away and picking accuracy. Not only does accuracy provide returns in better customer service it also lowers energy costs. An accuracy rate improvement from 95% to 98% over a million orders means 30,000 orders don’t have to be re-fulfilled. The effort expended from transportation, restocking, and more quickly adds up to significant energy reductions and cost savings.
An efficient distribution center amplifies all competitive advantages. From process improvements and smaller square footage requirements to limiting lighting needs use and enhanced order selection, the benefits of an automated distribution center mean a substantial energy cost reduction as compared to a traditional manual distribution center.
Recent Comments