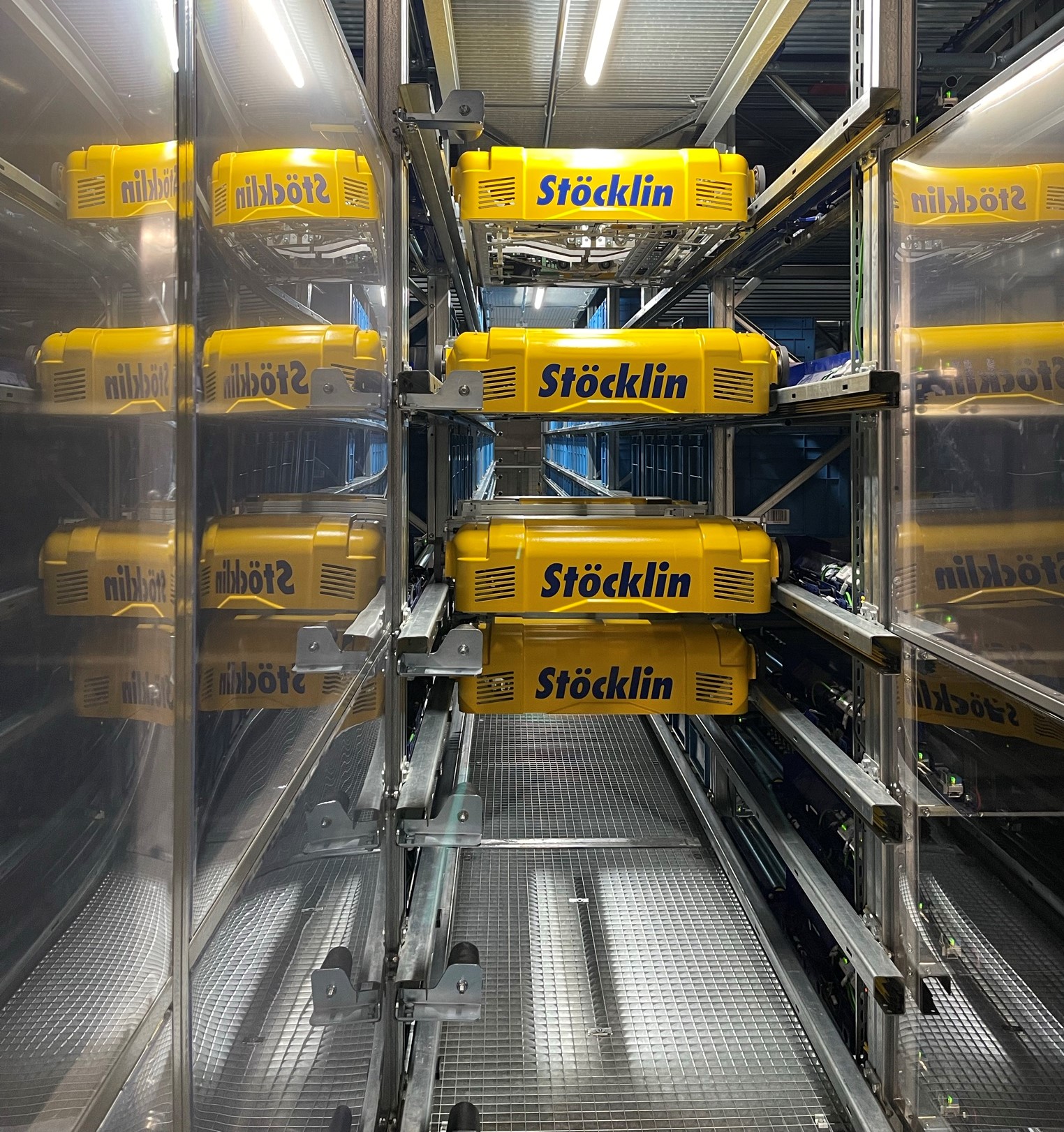
Flexibilty in Storage and Performance Delivers Quick Returns for Stöcklin Logistik Clients
In Laufen, home of the Technology Center of Stöcklin Logistik AG since May 2020, the Swiss intralogistics provider operates a state-of-the-art, fully automated spare parts warehouse for its in-house manufacturing facility. Only components from the company’s own production are used, including the FSP shuttle system, which is one of the newest additions to the product portfolio and is designed for high performance and maximum flexibility. This a scalable, comprehensive solution consists of racking, lifters, racks, conveyors and shuttle vehicles that can be adapted precisely to match individual system performance requirements.
“Swiss made” – as far as the eye can see: In the pallet warehouse, an automated storage and retrieval machine (ASRS) using the cranes from Stoecklin Logistik AG”s “MASTer” series, is moving pallets. Next to the pallet stacker cranes, the BOXer and the FSP shuttle system guarantee speed and precision in the automated small parts section of the warehouse, where totes and smaller containers are being moved. The high-performance lifter (BOXer/FSP) is flexibly adapted to the unique and individual performance requirements. Thanks to a sophisticated control concept, the shuttles adapt their dynamics to the container being transported. Slip compensation allows the shuttles to correct their position deviation during the travel and to drive safely to the destination. The conveyors pick up loads from the lifter or deliver them, and create a transfer point for the shuttles. The required output determines how the system is dimensioned and constructed. With Stöcklin Logistik AG’s experienced employees and engineers, each system is designed to meet the customer’s uniqe requirements.
As requirements change, systems can easily be modified and expanded
“Since the requirements for warehouse systems change over the years, the option for subsequent adjustments and extensions are essential,” says Urs Grütter, owner and CEO of Stöcklin Logistik AG. “We have taken the factor of flexibility into account in the development of the FSP, so that as order volumes increase or demands for further shorter delivery times grow, the performance can be adjusted accordingly. This in turn leads to a high degree of investment security for our customers.”
Redundancy, interchangeability, adaptability and fast accessibility ensure maximum availability, which is further increased thanks to reliable components and a coordinated control concept. The software, which can be integrated into existing warehouse management systems (WMS), coherently manages the orders that are processed by the aisle controller of the FSP system. The aisle controller ensures harmony among the components of the overall system and makes sure that the plant is operated in a process-safe manner.
Variability also guaranteed for totes and containers up to 100 lbs.
The FSP is designed to handle totes, cartons and trays weighing up to 50 kg (100 lbs). Standard totes can be stored double-deep with the One Width Shuttle (OWS) and various dimensions (min. 200x200x50 mm, max. 860x660x500 mm) (min. 7.8×7.8X1.9 inches, max. 33.8×25.9×19.6 inches) can be stored with the mixed multiple-deep Multi Width Shuttle (MWS) via a transversely adjustable telescopic gripper. The shuttle vehicles work simultaneously and independently of each other and are interchangeable if required, so that operations can continue uninterrupted in the event of a malfunction or maintenance. “Another advantage is that the system solution can also be integrated into existing structures thanks to its modularity and compatibility,” says Urs Grütter.
Flexibility through system-resilience even in times of uncertainty
The possibility of continuous scaling also offers the opportunity, for example, to efficiently map additional growth generated by an expansion of an e-commerce business at the logistics level. “Especially in times of dynamically changing environments, when creating accurate forecasts is very challenging, companies are increasingly dependent on being able to act with maximum flexibility,” adds Urs Grütter.
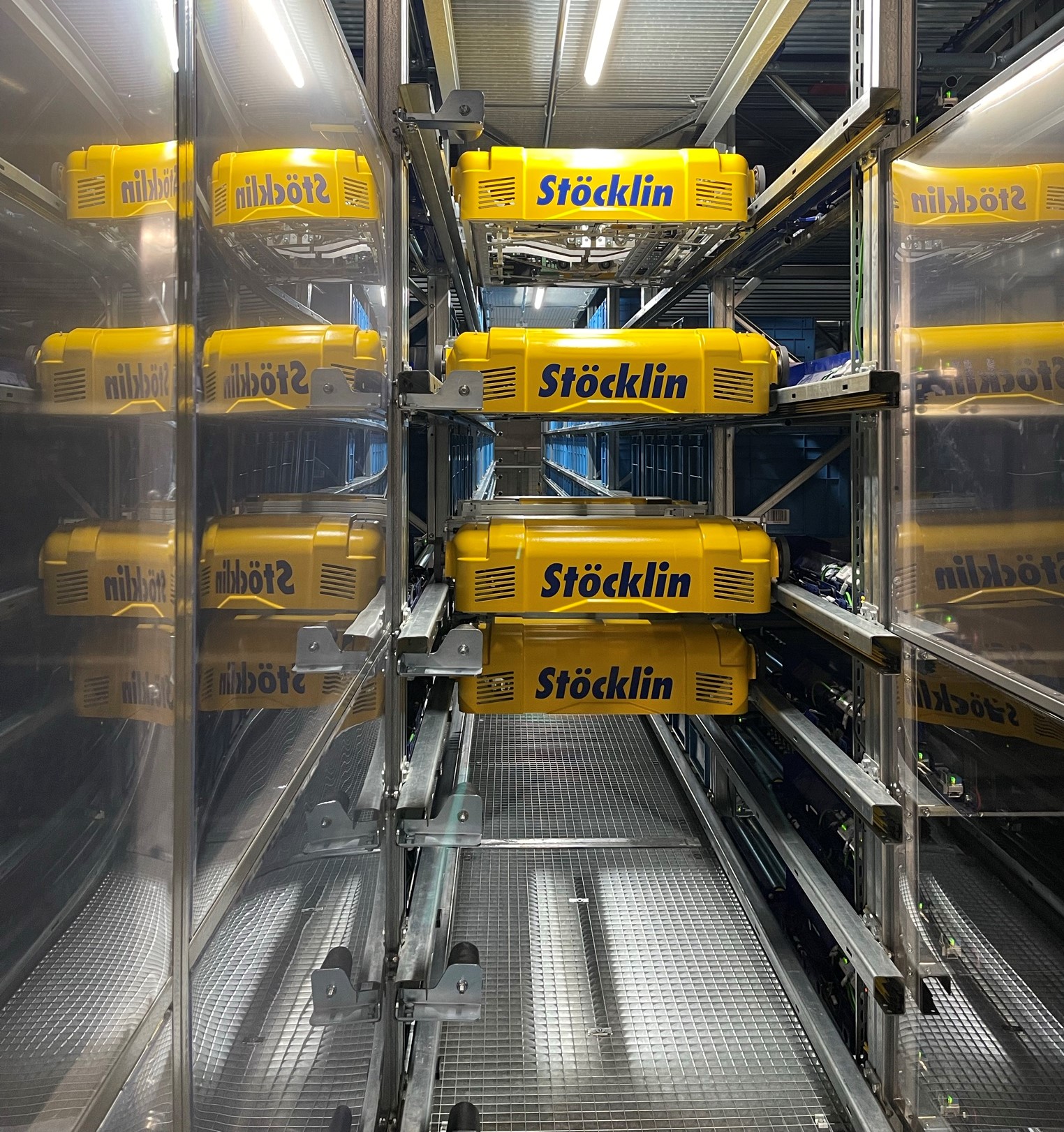
Recent Comments