Automated welding system ensures product quality and increases production efficiency
HAIGER/LAUFEN – Since the end of 2020, Stöcklin Logistik AG has been welding lifting platforms and mast modules for stacker cranes with a new 2-station robot system of Carl Cloos Schweisstechnik GmbH. After moving to the new HQ in Laufen in 2020, Stöcklin invested heavily in innovative manufacturing technologies. By switching to automated welding
technology, Stöcklin was able to significantly accelerate production processes, reduce non-productive time and raise the product quality to a new level. The new robot system consists of two stations that can be used flexibly for different components. On the larger station, the robot welds various mast modules that can vary in length from 10 to 36 ft. The individual components weigh up to 10 tons. When assembled, the masts can later reach a length of more than 130 ft.
On the smaller stations, various smaller components such as lifting platforms are manufactured. Due to the 2-station principle of the robot system, it is possible to insert the components in one station while the robot is welding in the other station – an enormous saving of time in the whole process run. Read more about our innovative technology center, with state of the art manufacturing equipment here.
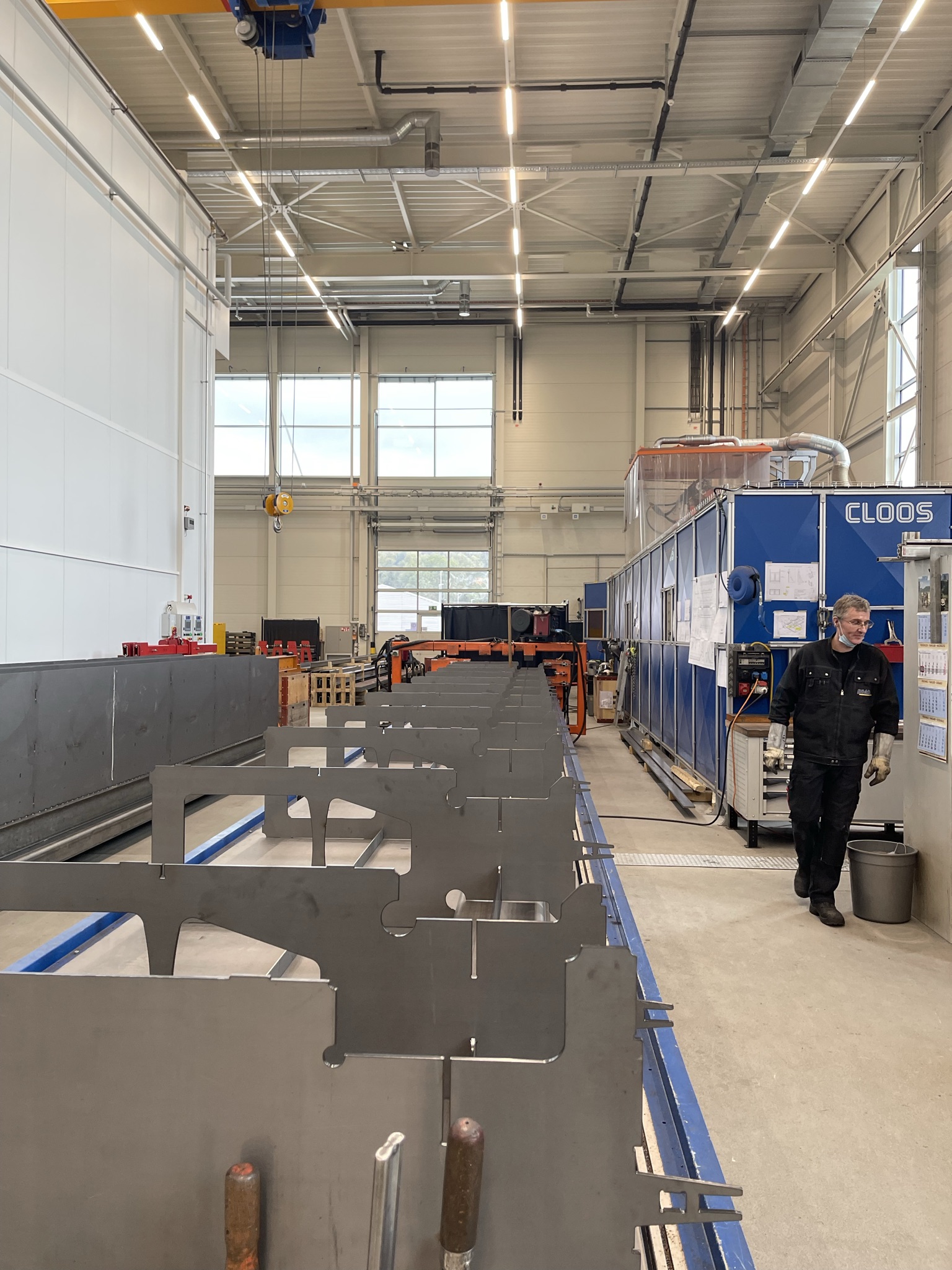
Recent Comments